TRIOL AT24 line UC
ऑर्डर स्थापित करें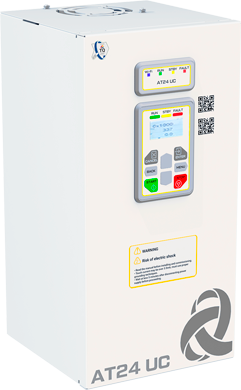
विशिष्ट लाभ
Control type
Vector sensor (closed-loop) and sensorless (open-loop) control
Encoders
3 different types of encoders supported
Motor parameters
auto-tuning of motor parameters with motor rotation and without it
Multi-tasking
Motor group control
Remote control terminal
Transient graphs
Quick settings
Settings via smartphone
उत्पादों के बारे में
Increased control accuracy
Variable Frequency Drive Triol AT24 line UС is an intelligent frequency drive for operating processes with high overload ability. There are all the advantages of Triol unique vector control algorithm implemented in Triol AT24 VFD line UC. Connecting three different types of encoders provides increased control accuracy to operate in a closed-loop system.
Easy set up
Setting up and controlling of Triol AT24 VFD line UC is easy due to the use of: Wi-Fi adapter with step-by-step Triol Wizard via smartphone, Service software Triol Drive for PC, Remote control terminal with transient graphs
विशेष विवरण
Input |
|
---|---|
Input voltage, V | 3х380 / 3х480/ 3×690 (-15 % …+10 %) |
Input frequency, Hz | 50 / 60 (-5 %…+5 %) |
Output |
|
Output current, A | 6.4 … 110 |
Output frequency, Hz | 0.5…400 |
Frequency resolution, Hz | 0.1 |
Acceleration / deceleration time, s | 1 …4000 |
Overcurrent characteristics | 150 % of rated value for 60 sec |
Efficiency, % | >97 |
Motor control |
|
Control methods | V/f (volts-per-hertz) (5 reference point) sensorless vector control (open-loop) sensor vector control (close-loop) |
PWM frequency, kHz | 2…10 |
Speed range | 1:100 in open-loop system 1:1000 in closed-loop system |
Speed accuracy (static) | ±10% of motor nominal slip in open-loop system ±0.1 % of rated speed in close-loop system |
Torque accuracy | ±10% in open-loop system ± 5 % in close-loop system |
Braking | By frequency
Coasting Dynamic |
Acceleration / deceleration types | S-curve, linear (3 reference points) |
Interface |
|
Terminal | Integrated seven-segment |
Light alarm | “Ready”; “Run”; “Control channel”, “Rotation” |
Push buttons | “Start”; “Stop”; “Fast access “ |
Control signals |
|
Customer supply | 10 V DC, up to 30 mA 24 V DC, up to 150 mA |
Number of discrete inputs | 8 |
Discrete inputs | Programmable |
Discrete inputs type | 24 V |
Number of relay outputs | 4 |
Relay outputs type | 250 V, 1 A |
Discrete output | 2 open collector |
Number of analog inputs | 2 |
Analog inputs | Programmable 0…10 V / 0…5 mA / 4…20 mA |
Number of analog outputs | 2 |
Analog outputs | Programmable 0…10 V / 0…5 mA / 4…20 mA |
Communication |
|
Physical Interface | 2 wire RS-485 for Modbus |
Communication protocols | Modbus RTU |
Frame transmission | 115200 bps by default 1200 -250000 bps |
Data format | 8 bits, 1 stop bit, no parity |
Number of addresses | 1…255 for Modbus |
Access | Slave |
Protection |
|
Supply protections | Phase loss, phase sequence fault |
Motor protections | Overcurrent
Overload Underload Phase loss Current unbalance Encoder open circuit Brake resistor open circuit |
VFD protections | Overload, Overheating, DC-link undervoltage, DC-link overvoltage, Power switch failure |
Insulation | Galvanic isolation between power and user circuits |
Insulation resistance | >1 MQ |
Configuration |
|
Braking IGBT-chopper | Up to 15 kw: built-in From 18 kW: option, built-in |
Wi-Fi adapter | Option, built-in |
Optional equipment |
|
Input line choke | Option, outdoor, by request |
Input passive harmonic filter | Option, outdoor, by request |
Braking resistors | Option, outdoor, by request |
Output sine filter | Option, outdoor, by request |
Output dV/dt filter | Option, outdoor, by request |
Construction |
|
Protection degree of Enclosure | IP21 |
Cabinet material | Up to 7.5 kw: plastic From 11 kW: steel |
Cooling | Forced air |
Noise level, @ 1 m, dB(A) | <75 |
Installation | Wall mounting |
Maintenance | One-side |
Cable entry | Bottom |
Operating conditions |
|
Operating conditions | Indoor, no caustic and volatile air, no dust |
Operating temperature | -10…+40 °C (-10…+104 F) |
Storage temperature | -40…+50 °C (-40…+122 F) |
Relative humidity, % | from 5 to 90 non condensing |
Altitude, m | up to 1000 m – rated power above 1000 m – with reduced power |
Functions
- Start / stop / reverse of motor with set acceleration and deceleration rates
- Auto-tuning of motor parameters (with rotation and without)
- PID-controller
- 2-wire control
- 3-wire control
- Automatic restart
- “Catch on the fly” mode
- Motor group control
- Operation by calendar
- Encoders supported – incremental, absolute, sine/cosine
- Accelerated passing of resonant frequencies (3 ranges)
- Recording the last 32 reasons of failures