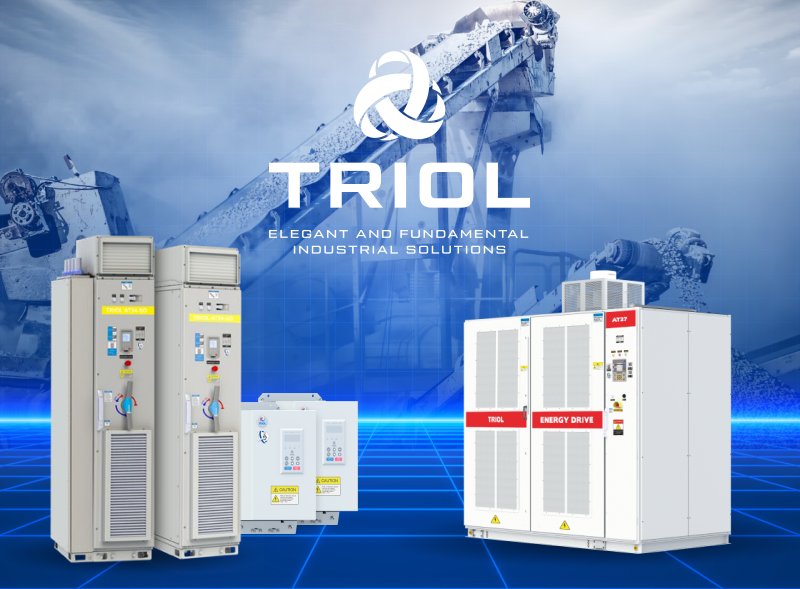
One of the main methods of cost optimization in production is the modernization and automation of technological lines.
The aim is to achieve the maximum possible reduction of energy consumption; to minimize equipment maintenance and repair costs; to increase the productivity of technological processes; and to ensure safe and uninterrupted operation of machines, mechanisms and infrastructure.
One of the ways to achieve these goals is the wide implementation of conveyor systems, which, in addition, provide additional convenience for personnel. Conveyors, transporters, escalators, and elevators help to ensure reliable and uninterrupted delivery of raw materials, semi-finished products, finished products, waste, and in some cases people, both horizontally and with a change of vertical level.
These are just some of the areas where conveyors are widely used and have often become integral parts of the process cycle:
- coal and ore quarries;
- metallurgy;
- food-processing industry;
- furniture manufacturing;
- mechanical engineering;
- chemical industry;
- textile manufacturing;
- polygraphy;
- processing of agricultural products.
According to the method of execution, conveyors can be divided into:
- conveyor belts;
- slat;
- scrapers;
- screw;
- roller conveyors;
- chain, etc.
Our challenges
1. Eliminating losses due to equipment downtime;
2. Reducing of production costs;
3. Increasing productivity of existing equipment;
4. Extension of equipment life;
5. Reducing maintenance costs;
6. Operation in conditions of high dust content and conductive dust environments;
7. Placement in limited space;
8. Adaptation to local ventilation and equipment maintenance capabilities;
9. Equipment integration into complete systems and modernization of systems.
Unscheduled conveyor downtime can bring losses associated with lost profits, through to the emergency shutdown of both an individual enterprise and critical infrastructure facilities that depend on the operation of conveyor equipment, for example, the shutdown of a thermal power plant due to a shortage of under-supplied coal.
To exclude the above problems, the AT24 and AT27 series variable frequency drives have the following solutions:
The kinetic buffering mode in AT24 and AT27 variable frequency drives ensures stable operation of Triol variable frequency drives in case of deep and unbalanced sags of supply voltage, and even at its complete loss.
In the kinetic buffering mode, the variable frequency drive operability is maintained by consuming a part of the kinetic energy of the rotating mechanism, followed by instantaneous restoration of the set operating mode of the mechanism when the power supply is restored. The time of operation of the VFD in this mode for conveyor drives can make 5-10 periods of supply voltage.
Triol VFD operation oscillogram with supply voltage loss
tbyp– bypassing time, 3.6 meter per sec.
ttp – transition process, 2.2 meter per sec.
Power cell bypassing oscillogram with HOpCoD™ technology bypassing block
The bypass of the AT27 power cell ensures uninterrupted operation of the variable frequency drive even if it is partially damaged. Triol Corporation offers a highly reliable solution to bypass a failed power cell in less than 4 meters per second. This is made possible by the unique, patented HOpCoD™ technology. Fast and reliable bypass of power cells allows the VFD to maintain operability and quickly restore the torque and rotation speed of the conveyor drive, which prevents the stoppage of the technological process and does not reduce the quality of the finished product.
Fan redundancy in the AT27 VFD allows the variable frequency drive to maintain operability even in the event of failure of up to 50% of all fans. The ventilation system has full fan redundancy. In the event of failure of one of the fans, the fan remaining in operation ensures removal of excessive heat.
Under each fan there is a gravitational louver unit that opens with the airflow when the fan is running. In the event of a fan failure, the gravity louvers close to circulate the cooling air as intended.
In order to reduce production costs, increase competitiveness in the market, and increase profits, the AT24 and AT27 series variable frequency drives provide the following solutions:
The vector control algorithm with magnetic flux optimization of the conveyor drive motor reduces the total power consumption of the motor, and together with the optimization of the technological process leads to a reduction in the cost of production.
The graph presents the result of measurement of the apparent power on different frequencies with the rated current.
Energy consumption decrease
Reducing losses of raw materials and semi-finished products in production
Tasks of coordinated operation of several conveyors
Task classification
Мaster Follower VFD Master Follower 1 Follower 2
Pic.1. Synchronizing two conveyors Pic.2. Synchronizing of conveyor belts
Pic.3. Electrical reduction: conveyor belts move at different speeds, the ratio of speeds is constant
When implementing a multi-conveyor system, there is a need to synchronize the drives of different conveyors. This is necessary to optimize the technological process and to avoid losses of raw materials and semi-finished products due to the unsynchronized speed of different conveyors.
AT24 and AT27 VFDs implement the functionality of multi-motor and multi-drive systems operating according to the "master-follower" principle, which allows the technological process to be optimized and avoids losses during transportation of raw materials.
Integration with ACS is provided by discrete and analog inputs/outputs, as well as serial communication ports with Ethernet, Modbus RTU, and Profibus protocols (optional).
AT24 and AT27 VFDs are adapted for operation together with APCS to provide the required technological process:
- energy-saving control of the conveyor drive (conveyor idle speed);
- increase in productivity of the conveyor in comparison with drives not equipped with VFDs;
- reduction of losses during production of finished products due to the synchronization of various sections of conveyor lines;
- provision of “master-follower” mode for two-motor drives;
- provision of conveyor reversal;
- conveyor positioning.
One of the most important tasks of the end user is the desire to increase the productivity of the processing plant without having to make significant investments in the plant’s fixed assets. For example, one of the weakest links in the mining industry may be a conveyor that capacity has been calculated based on the needs of the past and which does not meet the requirements of the time.
To solve this problem, the AT24 and AT27 series VFDs have the ability to run the drive motors at an increased frequency, which in some cases increases the conveyor performance by 10-20%.
Extension of the service life of the main equipment is an important challenge which reduces the cost of repair and replacement of worn-out equipment, which generally affects the growth of enterprise profits.
To implement this task, AT24 and AT27 series VFDs are provided with the following:
Vector control with author algorithms of torque limitation and motor speed control in Triol VFDs provides reliable motor protection from overload and shaft breakage, a specified starting torque, fast response to load changes on the motor shaft without loss of the specified speed, and accurate maintenance of the specified speed.
Starting at a current not exceeding the rated values allows the use of motor and VFD power cables with a smaller cross-section, reduces wear and tear, and extends the service life of the conveyor drive, and accordingly, reduces the cost of implementation, maintenance and repair of equipment.
In multi-motor systems, vector control allows load to be evenly redistributed between drives, which reduces wear and tear on conveyor drive mechanisms and extends the life of electric motors.
Torque limitation algorithm
The brake application and release at 200% torque limit setpoint without shaft block
Precise maintenance of motor torque and speed ensures that the specified speed at variable load is maintained until the load limit moment is reached, after which the motor speed is reduced when the torque limit algorithm is triggered, allowing the conveyor to remain operational when starting with a load or operating with a variable conveyor load.
The "Master-follower" function allows, by means of communication between the variable frequency drives, even distribution of the load between two or more motors, which prevents unacceptable overloading of some and inefficient use of other mechanisms, which in general affects the extension of service life of the main equipment.
Another solution from Triol is the use of low-voltage AT24 MP line VFDs. Independent control of each inverter with its own protection system provides flexible configuration of the complex to work both in single-motor and multi-motor systems, and integration into common mains allows the optimal distribution of power consumption between mechanisms depending on priorities.
The S-shaped acceleration allows shockless acceleration of the loaded conveyor, excluding shocks and dynamic loads on the motor, gearbox, and conveyor belt (excluding its breaks).
The Electromagnetic brake function reacts preventively in an emergency situation by urgently applying the electromagnetic brake on the electric motor shaft.
Conveyor sensor signal processing allows you to monitor the condition of the conveyor by sensors such as:
- Belt speed control sensor;
- Conveyor emergency stop sensor;
- Conveyor belt derailment sensor;
- Conveyor belt slack sensor;
- Conveyor belt overload sensor;
- Conveyor belt jamming sensor.
Control of these sensors and a prompt response to their signals makes it possible to react to the developing emergency or stop the accident before it starts, which avoids or significantly reduces repair costs.
Repair and maintenance costs are one of the most important items affecting the cost of production and profit of the enterprise. The AT24 and AT27 series variable frequency drives provide the following solutions to reduce repair time:
Reverse – this function allows you to reverse the direction of motor rotation, in order to direct the damaged section of the belt to the service site by the shortest path.
Reduced speed – this function allows you to pull the damaged section of the conveyor belt to the service area at reduced speed and also allows you to perform inspection of the conveyor belt for wear and damage.
Triol AT27 MV line with IP66 (NEMA4) protection is a solution for applications with high dust content and very often conductive dust. The VFD has a dedicated cooling channel to ensure trouble-free and reliable operation of the frequency converter even in the most difficult conditions.
Triol AT24 MP line with liquid cooling provides the ability to operate in confined spaces and rooms without ventilation.
Triol AT24 SD line – Compact solution for heavy-duty applications. With dimensions of only 750x450 mm in plan, and power up to 630 kW. Allows you to place the equipment in an environment of limited space.
Triol VFD AT27 ED line has the smallest dimensions in the world among variable frequency drives of the 6-11 kV class!
The AT27 ED line variable frequency drive saves not a few tens of centimeters but on average 25-30% of the area occupied by the VFD.
The modular design of AT27 FC allows cleaning and replacement of air filters without stopping the VFD while ensuring the safety of personnel, and repair time is minimized due to modern design solutions and the interchangeability of power cells.
The location of the cooling fans exclusively on the roof makes it easy to organize the heat dissipation of the Triol VFDs by connecting the ducts directly to the roof of the drive converters around the fans. The heat generated by the converter in operation will not heat up the room but will be immediately discharged from the room, ensuring long and trouble-free operation of the unit.
The versatility of Triol AT24 SD line variable frequency drives allow them to operate in 380/480/690 V mains, as well as with step-down transformers of our own production at 6 and 10 kV. Because of this, AT24 SD line variable frequency drives are perfect for new lines as well as for modernization of existing facilities.